Warehouse safety: how to ensure safe working conditions?
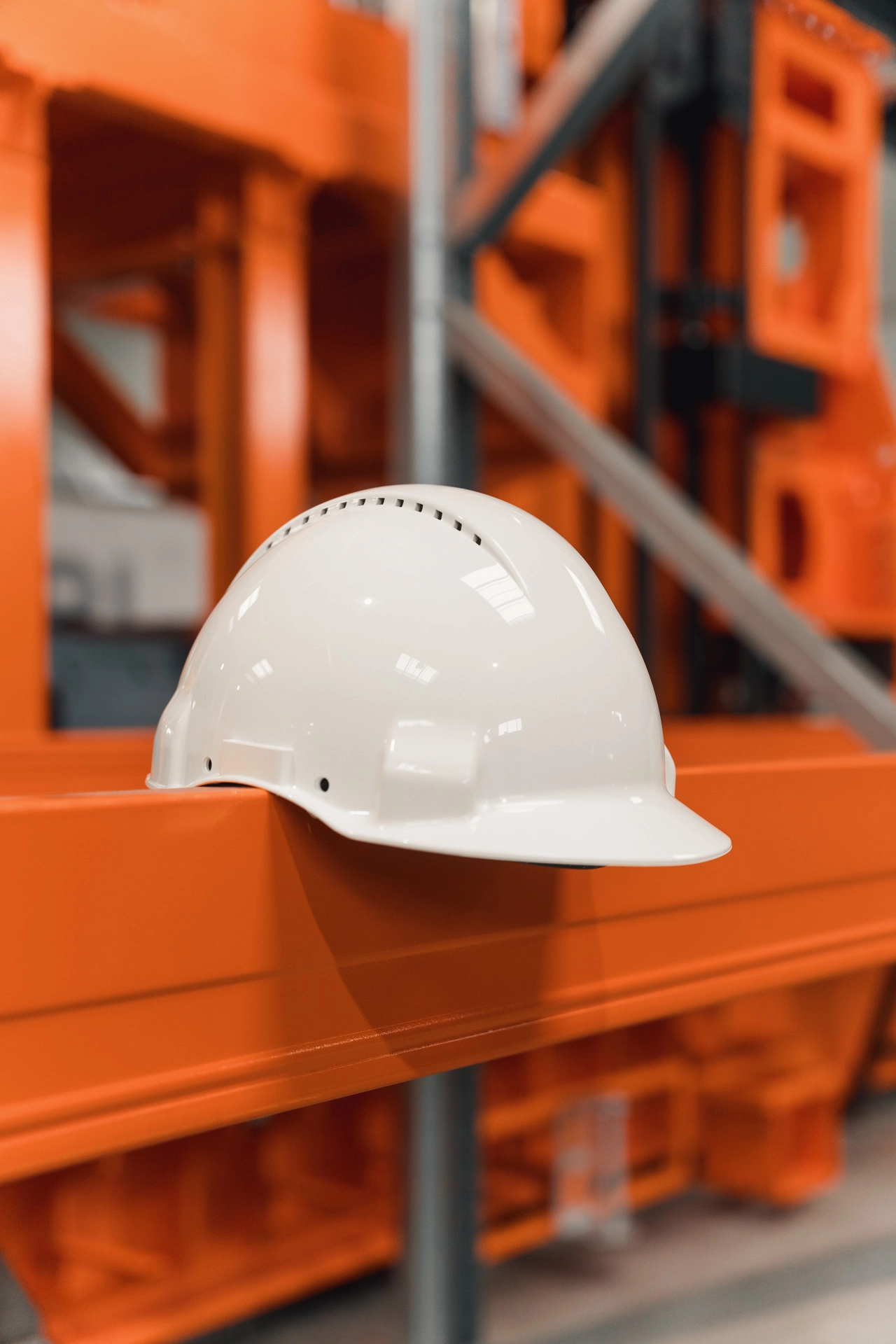
The implementation of occupational health and safety regulations in a warehouse is extremely important for creating a safe workplace. Space planning must comply with applicable regulations, which include, among others, road width, lighting, heating, ventilation and personal protective equipment. What are the most important occupational health and safety regulations in a warehouse?
Occupational health and safety regulations
Occupational health and safety regulations in Poland are regulated by, among others, the following legal acts:
- Regulation of the Minister of Labour and Social Policy of 26 September 1997 on general occupational health and safety regulations - specifies generally applicable occupational health and safety regulations in workplaces, which in particular apply to buildings, work premises and premises of workplaces, work processes and sanitary and hygienic rooms and devices.
- The Act of 26 June 1974 - Labour Code - Section X of the Act entitled Occupational health and safety regulates, among others, basic obligations of the employer, rights and obligations of the employee, construction and work premises, machines and other technical devices, factors and work processes posing a particular risk to health or life, accidents at work and occupational diseases, training, personal protective equipment and work clothing and footwear.
EU health and safety regulations
Warehouses in Poland must comply with EU directives implemented into Polish law, including the above-mentioned legal acts. On 15-16 May 2023, the EU summit on occupational health and safety was held in Stockholm - its task was to set goals by 2027. During the event, it was confirmed that the Framework Directive 89/391/EEC on the introduction of measures to improve the safety and health of workers at work is the gold standard for employee protection in the European Union.
Other EU legal acts concerning occupational health and safety include:
- Directive 89/654/EEC – concerns health and safety at work,
- Directive 2009/104/EC – concerns the use of work equipment by employees during work,
- Directive 89/656/EEC – concerns the health of employees using protective equipment,
- Directive 2003/10/EC and 2002/44/EC – concern exposure of employees to risks caused by physical factors (noise or vibration),
- Directive 2000/54/EC – concerns risks related to exposure to biological factors at work.
The most important occupational health and safety regulations in the warehouse
The occupational health and safety regulations cover all industries and apply to every company employing employees. However, let us focus on the occupational health and safety regulations in the warehouse, especially those that have the greatest impact on ensuring safe working conditions.
Fire protection systems in the warehouse
Every warehouse must be equipped with appropriate fire protection measures that will detect threats at an early stage, alert the services and people in the rooms. These include, among others, fire switches, fire alarm systems, smoke detectors and thermal sensors. The presence of equipment that will increase the safety of employees is also mandatory in the warehouse, these are fire protection devices such as fire extinguishers. Fire protection devices must not only be available, but also functional, so it is important to remember about regular legalization, e.g. fire extinguishers and efficient repair in the event of a failure of the devices. It is also important to install fireproof doors, which - depending on the class - are fire resistant. For example, EI 30 doors must be able to prevent fire from spreading for at least 30 minutes. The E and I markings refer to the product's fire tightness and insulation, respectively.
It is also necessary to comply with the technical and construction, installation and technological requirements in order to prevent fires. It is absolutely necessary to comply with the regulation that evacuation routes must always be accessible - so they cannot be blocked with pallets and devices that would hinder a possible evacuation. Every newly hired employee must also undergo health and safety training containing information on fire protection.
Health and safety regulations - high storage
A high storage warehouse is considered to be a racking system with a height of 7.2 m to even 50 m. Such facilities allow for the optimal use of storage space - up to the ceiling. Warehouses are increasingly automated and professional technical solutions are used in them, such as elevators, trolleys and stacker cranes. Warehouse work in high-bay warehouses mainly includes storage and transport, unloading and loading of goods, operating intra-warehouse transport equipment, as well as manual handling of goods.
Basic health and safety regulations covering high storage:
- organising appropriate space for storing goods,
- defining techniques for storing goods in the warehouse,
- establishing the permissible storage height,
- establishing the permissible load weight for shelves, floors, etc.,
- clear marking of routes, shelves and devices,
- securing shelves against tipping over,
- adjusting the distance between shelves to the regulations and the means of transport used,
- placing instructions specifying the method of work in the high storage warehouse,
- installing appropriate lighting, ventilation and heating systems,
- training employees,
- adjusting the temperature to the specifics of the stored goods,
- using means of transport that meet technical requirements.
Prohibited activities in high-bay warehouses include:
- storing loads in places not designated for this purpose
- leaving machines and devices running without supervision, the instructions of which do not allow this,
- operating machines and devices by unauthorized persons,
- exceeding the permissible loads for racks or floors.
Transport routes and equipment
Storage rooms must be adapted to the type of goods stored, and access to the racks should be not only safe, but also convenient. Transport routes should be marked in a visible manner - using continuous white or yellow stripes. The width of the routes must be adapted to the type of traffic (one-way or two-way) and vehicles, which should be able to perform free maneuvers. Any obstacles on the road, such as thresholds or steps, should also be marked to increase safety in the warehouse. The racks used must meet the appropriate requirements regarding strength and load-bearing capacity. The warehouse equipment must be kept in good technical condition, used in accordance with the instructions and regularly maintained.
Protective and work clothing
Employees' safety is also ensured by personal protective equipment, footwear and work clothing. In warehouses, helmets, safety footwear, harnesses, gloves, safety glasses, ear muffs and reflective clothing are most commonly used (depending on the working conditions and scope of duties). The employer is obliged to provide the employee with free personal protective equipment, work clothing and footwear that meet the requirements specified in Polish standards. The employer cannot allow the employee to work without these items and the work clothing and footwear required for a given job position. In addition, the employer is obliged to wash, maintain, repair, dedust and disinfect the assigned personal protective equipment, work clothing and footwear. However, the washing of work clothing may be performed by the employee, who is entitled to a cash equivalent for this.
Health and safety rules – who can work in a warehouse?
Every person working in a warehouse must undergo appropriate health and safety training. It is also important to pay attention to who we employ to perform specific duties.
Requirements for people employed in a warehouse:
- 18 years of age or older,
- at least primary education,
- UDT qualifications for forklifts (if their operation is part of the employee's duties),
- valid health and safety training,
- current medical examinations,
- no contraindications to work in a given position.
People working in warehouses are more exposed to accidents than office workers, so the employer may also require completion of a first aid course, which can be combined with health and safety training.
What are the basic mistakes that threaten safety in a warehouse?
The most common mistakes include:
- not wearing a helmet or appropriate work clothing,
- not using equipment for its intended purpose,
- exceeding the load capacity of equipment for short-range transport,
- exceeding the permissible speed of forklifts,
- leaving machines and equipment unattended,
- operating machines and equipment without authorization,
- blocking evacuation routes,
- using faulty equipment,
- not carrying out important inspections of machines, equipment and fire extinguishers.
Occupational health and safety regulations in the warehouse are intended to increase employee protection. Ensuring compliance with Occupational Health and Safety regulations is not only a way to avoid accidents at work, but also high fines that may be imposed on the company by the National Labor Inspectorate or the Office of Technical Inspection.
Are automated warehouses safer?
Automated warehouses are generally considered to be much safer than their manual counterparts, where most operations are performed by people. In manual warehouses, the so-called "human factor", which carries the risk of errors such as forklifts hitting shelves, goods falling from height, trolley collisions or employee knocks. In addition, work ergonomics are often overlooked, which can lead to musculoskeletal system overloads. In automated warehouses, the risk of such accidents is minimized, because most operations are controlled by sensors and systems. The role of humans is mainly limited to supervision and operation, and potential operator errors are secured by systems that prevent accidental actions, e.g. on control panels. Additionally, automated warehouses can remind about necessary maintenance activities, monitor machine wear and tear and perform efficiency tests, which increases their reliability and safety.